Acoustic voxels: Manipulating sound waves makes possible acoustic tagging and encoding
Manipulating sound waves can be a powerful tool with wide-ranging applications in medicine and surgery, materials science, pharmaceuticals, to name a few. But sound wave manipulation is not easy. Each wave contains many frequency components, and waves bounce off objects in complex ways depending on the shape or material of the obstructing object. Most recent progress in manipulating sound waves involves controlling sound waves created at specific frequencies. Manipulating sound waves in a customized way is much more challenging, but now a team led by Changxi Zheng has done exactly that. Using computational techniques, Dingzeyu Li (Columbia), Disney Researcher David Levin, and MIT professor Wojciech Matusik working with Zheng have developed a method to predict and manipulate sound waves as they pass through an air chamber such as those found in wind instruments and mufflers. The method involves building chambers out of small primitives called acoustic voxels that can be rapidly modified to change acoustic characteristics. It is a general approach that works for both musical instruments and industrial mufflers. More interestingly, it leads researchers in a completely new direction: acoustic tagging for uniquely identifying an object, and acoustic encoding for implanting information (think copyright) into an object’s very form. Much more may be possible.
Building objects with customized acoustics to both identify an object and relay information about it had not been the original goal. The project began as an extension of a previous one from last year when Changxi Zheng and his team used computational methods to design and 3D-print a zoolophone, a xylophone-type instrument with keys in the shape of zoo animals. While an original and fun musical instrument, the zoolophone represents fundamental research into vibrational sound control, leveraging the complex relationships between an object’s geometry and the vibrational sounds it produces when struck. The researchers start with a sound in mind and then computationally search over a large shape space for the exact geometry of a particular zoo animal shape that can produce the desired sound.
Zheng and his team this year turned their attention from striking instruments to wind instruments, which produce notes using a different principle: as sound waves pass through a chamber, they reflect back and forth off the sides of the chamber; this boosts certain frequencies in such a way to produce a specific note.
In theory, the sound passing through a chamber can be controlled by changing the chamber’s shape, but connecting sound characteristics with a chamber’s shape is not intuitive; for this reason, the chamber is almost always a tube or other simple shape whose acoustic properties are relatively easy to understand and easy also to manufacture. Even the simplest shape, however, often requires post-production tweaking to achieve the desired acoustic results.
Sound propagation is complex, but it can be understood and analyzed computationally, opening the door to more complex chamber shapes that can produce a broader range of sounds; and with 3D printers today, even complex shapes can be fabricated with little effort.
Freed from having to keep things simple, the researchers could re-imagine acoustic filters, concentrating on the best way of fitting a filter within an arbitrary 3D volume while achieving target characteristics. The simple but laborious process of creating and tweaking a tube-shaped chamber is formulated as a complex, computationally intensive problem of solving acoustic wave equations (or in the frequency domain, the Helmholtz equation) while searching over a huge search space for the exact chamber shape that can produce the target sound.
The solution was the acoustic voxel, a small, hollow, cube-shaped primitive through which sound enters and exits. Designed to be modular, voxels connect to form an assembly via circular insets on each side that can be opened to provide an exit or entry point, forming an infinitely adjustable graph-type structure. Changing one of several parameters—the number and size of voxels or how they connect—changes the acoustic result.
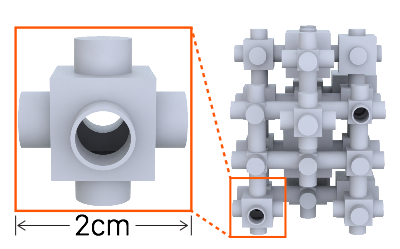
The entire assembly can be complex, but each individual voxel has a simple structure, which makes it possible, when solving equations, to separate out and precompute the transmission matrices that help to quantitatively describe a voxel’s acoustic filtering behaviors. By precomputing matrices, which are stored in a database and retrieved at runtime optimization, researchers realized a 77kx speedup over a standard method (finite-element method) that does not involve precomputations. What would normally take hours instead takes one or two seconds. (Testing done at Bruël & Kjær Laboratories showed that the computer simulations using transmission matrices closely matched results obtained using traditional, high-end lab instruments.)
The technical details of method are described fully in the paper Acoustic Voxels: Computational Optimization of Modular Acoustic Filters, but the overall method works generally as follows: Given three inputs: (1) the desired acoustic result, (2) a 3D volume in which to encapsulate the acoustic filter, and (3) the locations of the inlet and the outlet, the method specifies the size and number of voxels and how they should be assembled. The process is completely automated and optimized (via hybrid method that interleaves a stochastic optimization with a gradient-based quasi-Newton scheme). Even novices can design and fabricate objects with specified acoustics.
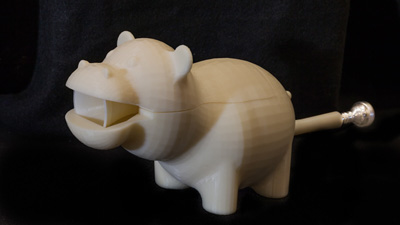
Because a voxel assembly can fit into any specified area, the shape of the object that contains a voxel assembly can be arbitrary. A trumpet doesn’t have to look like a traditional trumpet; it can be the shape of a cartoon hippopotamus and still produce trumpet notes.
Industrial and automotive mufflers also have an acoustic chamber, as do sound-suppressing earmuffs. It was an easy extension of the acoustic voxel method to target transmission loss in a frequency range and thus suppress, or muffle, certain frequencies.
Acoustic voxels thus expand the range of acoustic filters, providing a more generalized filtering approach that has application in both the creative realm of new music instruments and the stringent engineering requirements of automotive and industrial mufflers, two areas that previously required separate design and manufacturing.
Manipulating sound waves to embed ID and other information
Acoustic filters work by manipulating sound waves, and acoustic voxels give researchers a way to exactly control that manipulation. It soon became clear to the researchers that the potential uses of acoustic voxels extended far beyond filtering, and led them in an entirely new direction with wide-open implications: acoustic tagging to uniquely identify a 3D-printed object, and acoustic encoding to implant information in an object’s acoustics.
A unique voxel assembly produces a unique acoustic signature. Two objects may have the exact same exterior appearance but if their hollow interiors contain different voxel assemblies, each object, when struck or tapped, produces a sound unique to that object. Using an iPhone app created for the purpose, researchers recorded the sound made by objects with different voxel assemblies and used these recordings to accurately identify each object.
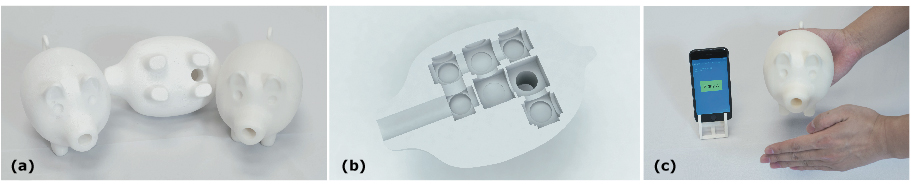
Acoustic tagging could complement QR codes and RFID tags, both of which entail operations entirely separate from manufacturing: printing labels (or in the case of RFID tags, attaching electric circuits in a post-process), matching them to the right object or part, and finally affixing them.
Acoustic tags instead come directly out of the 3D fabrication; ID information is “built-in,” saving the time, effort, and expense of individually labeling parts, especially helpful when building larger mechanisms or structures out of hundreds or more separate pieces.
Acoustic voxels can do still more. If a chamber can manipulate sound waves to boost or suppress frequencies, it can manipulate waves also to encode a string of binary bits and thus relay information such as copyrights or other product information. The researchers show how a “1” for instance might be encoded if frequency loss falls to a certain level at a certain location in the sound wave while a “0” might be indicated by a frequency change in a different location.
Protecting copyrights, patents, or trademarks is a growing concern for 3D printing, where it can be hard to tell an illegal counterfeit from the protected original (such as figures from Disney, Marvel, or other companies). Acoustic voxels show how information and identification can be embedded into the acoustics of an object, requiring no additional procedures or labor.
But the promise of acoustic voxels extends even further, leading Zheng and his team in still another direction.
The current acoustic voxel project is for fabricating sizable objects producing audible sounds. Zheng is already investigating how voxels might be used to control ultrasound waves, hinting at the intriguing possibilty of acoustic cloaking, where sound waves are diverted to hide objects from being detected through acoustical means. Applications range from hiding objects from sonar to disguising obstructions that block sound waves, such as in auditoriums and other spaces.
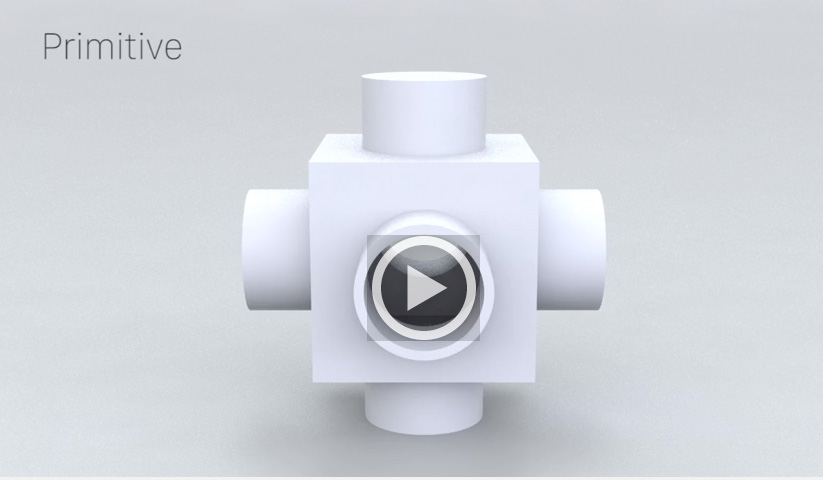
Posted 7/18/2016
– Linda Crane